Advantages:
- PLCs with protection against extreme climates, vibration, impacts and surge voltages.
- They are fieldbus-independent and ideal for decentralized fieldbus systems.
- Embedded Linux® operating system and e!RUNTIME based on CoDeSys 3
Reliable under Extreme Conditions: the PFC200 XTR Controller
The PFC200 XTR Controller for extreme environments and Ex areas: engineering, controlling and visualizing where other controllers fail!
With the PFC200 XTR Controller, WAGO offers a rugged device that excels in extreme environments. Requiring no additional protective equipment, the controller withstands temperature fluctuations from −40 to +70°C (−40 ... +158°F), has extreme resistance to impulse voltage up to 5 kV, is immune to interference and is vibration-proof up to 5g. Thanks to the e!RUNTIME environment based on CODESYS V3 and the real-time-capable Linux® operating system, this PLC is the efficient controller for your automation tasks. This includes locations that demand more than a typical automation system can provide.
The Benefits for You:
- CODESYS V3 runtime system
- Comprehensive range of XTR components for extreme environments
What Makes the PFC200 XTR Controller Successful
Extremely Rugged
The PFC200 XTR is unfazed by both freezing cold down to −40°C and scorching heat up to +70°C (−40 ... +158°F). The maximum approved operating altitude of 5,000 m is another highlight. Even in the thin air of a mountain-top station, the system impressively demonstrates its high performance and availability. The PFC200 XTR provides greater immunity to impulse voltages up to 5 kV, lower EMC emission of interference and higher insensitivity to EMC interference, ensuring trouble-free operation in virtually any application.
Embedded Linux
Embedded Linux is available for users who are ready to take complete control and prefer using a lean and secure operating system directly. This real-time Linux® software provides a wide range of advantages, including the flexibility of adapting open-source code to the user’s specific needs at any time. In addition to being highly stable, this robust operating system also benefits from continuous optimization by the active open-source community, keeping you both up to day and ready to adapt to what’s next – especially when it comes to security.
CODESYS V2 and V3
Thanks to the e!RUNTIME environment based on CODESYS V3 and the real-time-capable Linux® operating system, this controller is the efficient control system for your automation tasks, even in locations that demand more than a typical automation system can provide. This controller also stands apart because it includes two operating systems: You can choose to use either the e!COCKPIT engineering software based on CODESYS 3 or WAGO-I/O-PRO based on CODESYS V2 to design your projects.
Telecontrol Protocols
The PFC200 variants can also be used as telecontrollers. In addition to the IEC 60870-5-101, -103, -104, IEC 61850 and IEC 61400-25 telecontrol protocols, they also support the DNP3 communication standard. Even the interfaces are compelling: The PLC is available in two versions with different numbers of communication interfaces – either two ETHERNET connections and an RS-232/RS-485 interface or two ETHERNET connections, RS-232/RS-485, CAN, CANopen and PROFIBUS DP slave interfaces.
Engineering, Control and Visualization in Extreme Conditions
Thanks to the e!RUNTIME environment based on CODESYS V3 and the real-time-capable Linux® operating system, this controller is the efficient control system for your automation tasks, even in locations that demand more than a typical automation system can provide. The PFC200 XTR Controller also stands apart because it includes two operating systems: You can choose to use either the e!COCKPIT engineering software based on CODESYS V3 or WAGO-I/O-PRO based on CODESYS V2 to design your projects.
Fast and Cost-Effective Operation of Machines and Systems
In addition to the well-established CODESYS V2 runtime system, the PFC200 Controller also features the CODESYS V3-based e!RUNTIME system. This allows the controller to perfectly support the transition to CODESYS V3. Using this convenient and simple runtime system along with the integrated Web visualization application, you can quickly and efficiently carry out even complex automation tasks. The controller satisfies the requirements of traditional engineering disciplines, such as mechanical engineering, while tackling the toughest technical demands of fields like power supply, shipbuilding and the on/offshore industries.
Large Memory, Fast Processor and Numerous Communication Interfaces
The features are impressive: Despite its compact size, WAGO’s programmable logical controller (PLC) carries all the vital interfaces and even includes two RJ-45 and RS-232/RS-485 ports, depending on the version you select. The ETHERNET interfaces can be configured independently, meaning two separate networks can be configured with the PLC. The two ETHERNET ports can function as an ETHERNET switch to create a line topology. The SD card slot provides additional functionality, such as allowing large image files to be stored on an SD card for Web visualization.
The rugged plastic controller housing includes a Cortex A8 processor with speed up to 1 GHz, along with up to 512 MB of RAM for exceptionally high operating speeds. The largest possible program and data memory of 1.5 GB also provides the PFC200 with sufficient reserves for complex control tasks. Large memory, a fast processor and numerous communication interfaces for complex control tasks.
Easy Familiarization, Easy Switchover from Other Programming Languages
Incorporating the well-established CODESYS industrial standard makes initial startup even faster. Besides six different IEC 61131 programming languages (IL, LL, FBD, ST and FC) and CFC, ambitious users can also write their projects in C/C++, PHP or shell scripts. Programs and libraries created in any type of programming language are compatible with CODESYS applications.
Fast Fieldbus Configuration
The CAN, CANopen, PROFIBUS DP and Modbus TCP/UDP/RTU protocols allow flexible connection to fieldbus systems and external input/output devices. These fieldbus systems can be configured directly in the e!COCKPIT network view. The ETHERNET interfaces also support all common protocols such as DHCP, DNS, NTP, FTP and HTTP. A secure connection is provided via SSH, HTTPS and FTPS.
Interference-Free and Secure Connection via OpenVPN and IPsec
The controller connects to the mobile network via encrypted Virtual Private Network (VPN) access and supports both the OpenVPN and IPsec protocols. A VPN tunnel connects the controller to the network via GPRS and transmits all the data encrypted via SSL and TLS, ensuring perfect protection of the data against unauthorized access. The VPN can also be configured using the Web-Based Management on the controller.
Products
Any control task, large or small, must be cost-effective. WAGO has the right controller for every task and requirement.
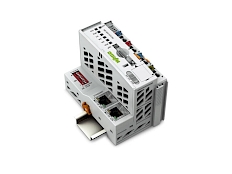
Maximum Performance in Minimum Space: The PFC100 Controller
A variety of outputs in one compact housing! With the PFC100 PLC, WAGO offers a very well-equipped controller with a compelling cost-benefit ratio.
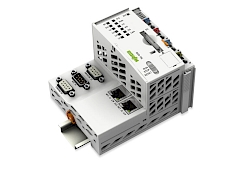
Our Most Powerful Line of Controllers: PFC200
WAGO's PFC200 Controllers are ideal for a wide variety of applications in industrial, process and building automation.
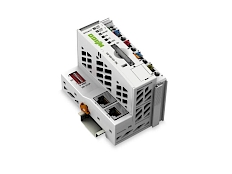
Our Most Versatile Controllers: Controllers 750
WAGO's 750 Series Controllers are ideal for a wide variety of applications in industrial, process and building automation.

For Extreme Environments: 750 XTR Controllers
Automation without limits in extreme environments – the 750 XTR Controllers
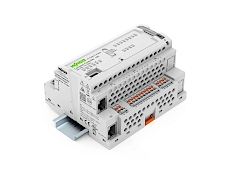
Maximum Performance in Minimum Space Compact Controller 100
The new Compact Controller with integrated I/Os is perfect for smaller automation solutions.